Welding and Riveting are two techniques that are great for joining metals. While both are great for metal fabrication, each of them has its specific use and purpose. But sometimes one question that often comes up with these two techniques is “Is welding more expensive than riveting?
Well, the answer isn’t that straightforward. That’s why, we have brought a detailed guide on this. Here we will break down the cost factors for both welding and riveting.
Welding
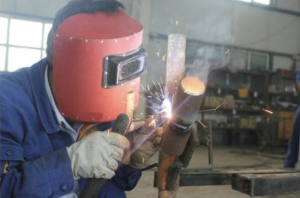
Welding is a fabrication process that joins materials, usually metals or thermoplastics, by causing fusion. It is a process that has been refined over decades and is widely used in various industries, from automotive manufacturing to aerospace engineering.
The Welding process
Welding involves melting the base materials and often adding a filler material to form a pool of molten material (the weld pool) that cools to become a strong joint. This process creates a permanent bond between the materials.
Skill Requirements
Welding is a skilled trade that requires extensive training and practice. Welders must understand various techniques, material properties, and safety procedures. Certification is often required for professional welders.
Welding Benefits
- Stronger joints: Welding typically creates joints as strong as or stronger than the base materials, providing excellent structural integrity.
- Versatility: Welding can join a wide range of materials and thicknesses, and can be used to create complex shapes and structures.
- Watertight seals: Welded joints can create airtight and watertight seals, which are crucial in many applications like pipelines or pressure vessels.
- Weight reduction: Welded structures often weigh less than equivalent riveted structures, which can be advantageous in industries like aerospace and automotive.
- Aesthetics: Welding can produce seamless joins, which can be desirable for a clean, modern look in visible applications.
Riveting
Types of Riveting
Riveting is a mechanical fastening process used to join materials using a rivet – a permanent mechanical fastener. This method has been used for centuries and remains relevant in many industries today.
The Riveting Process
Riveting involves inserting a rivet through aligned holes in the materials to be joined. The tail of the rivet is then deformed, creating a second head that holds the materials together.
Types of Riveting
There are several types of riveting, including:
- Solid Riveting
- Blind Riveting (or Pop Riveting)
- Semi-tubular Riveting
- Full Tubular Riveting
Equipment
Riveting equipment is generally simpler than welding equipment. It may include:
- Rivet gun
- Hammer and bucking bar
- Drill
- Rivets
Skill Requirements
While riveting does require skill, it generally requires less training than welding. Many riveting tasks can be performed by workers with minimal specialized training.
Riveting Benefits
- Joining dissimilar materials: Riveting excels at joining materials that can’t be easily welded, such as certain combinations of metals or metal-to-metal joints.
- Lower equipment costs: Riveting generally requires less expensive and simpler equipment compared to welding setups.
- Ease of inspection: Riveted joints are typically easier to inspect visually, simplifying quality control processes.
- Lower skill requirements: Riveting often requires less specialized training than welding, potentially reducing labour costs.
- Preserves material properties: Unlike welding, riveting doesn’t involve heating materials to their melting point, which can help preserve the original properties of heat-treated or tempered materials.
If you have any question please feel free to contact: Joyce@beisi-rapid.com